How to Reduce Material Removal Cost by 30% or more on CNC machine with Virtual Machining Tools
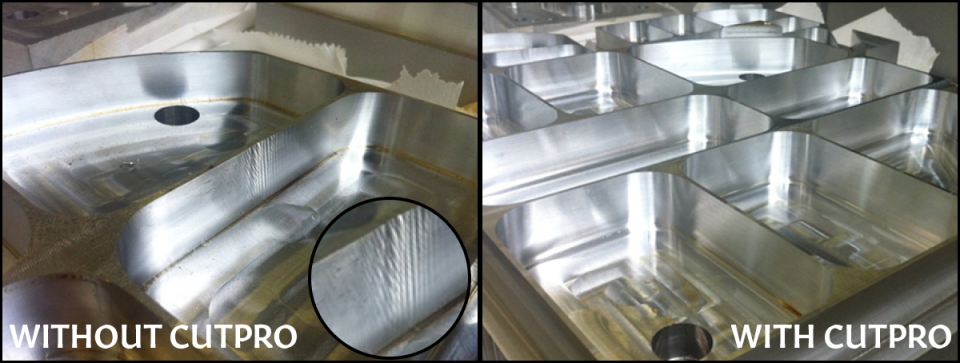
Virtual machining and pre-production simulation offers great improvements in reducing material removal costs on the CNC machine.
The system also helps to reduce the production cycle in terms of man-hour, machine-hour, machine downtime and scrap rates.
So, what is virtual machining and how does it help reduce the production costs?
Virtual Machining
In CNC machine production, optimization takes time and effort and if the process is not controlled, may cause loss of time and money in the process.
In common practice, certain trials and tests are made to find the optimum (or close to optimum) settings to work on any given material and design. However, virtual machining is the ultimate solution to reduce or eliminate these costs.
Great! But then how does the system work?
A virtual machining system gets all the information of the CNC machine (whatever the model is), analyzes the system (tap testing), and combines this information with material specifications and tool geometry. Then, the system proposes the most productive set of spindle speed, depth, width and feed without chatter vibrations and violation of torque and power limits of the machine. Instead of costly physical cutting tests, cost-free virtual cutting tests can be carried out to predict forces, vibrations, torque, power, surface form errors.
Another very important benefit of the system is minimizing the scrap rates, especially when machining high cost – low volume parts by eliminating blind trial cuts.
What Are the Actual Results?
Virtual machining has been the strongest tool in competition for its users. Hence, many of our clients use our virtual machining solution CutPro in their production cycle and have managed to reduce costs substantially.
Aircraft Parts
Typical monolithic aircraft parts are machined from solid or forged blocks, where 95% of the raw material is milled away. We received cycle time savings between 15% to 70% depending on the workpiece shape and NC program settings. As we are not able to share the customer’s factory results, our experienced aerospace machining engineers conducted a test in our laboratory.
During the test, in a normal production cycle, the costly aircraft part was scrapped twice during the trial cuts. But when CutPro is applied, the part was not scrapped and the cycle time was reduced by 50%. (REF: the pic above shows with and without CutPro results)
Difficult Parts Production Solution
A die maker in Japan had to use a very long stick out for a ball end milling of a deep, sculptured cavity. Therefore, due to excessive chatter vibrations, the depth of cut and spindle speed was extremely low. With CutPro, the optimal speed and depth of cut were predicted, and the material removal rate was increased by 17 times!
High Return on Investment
CutPro is the most innovative and effective virtual machining solution for process planners in the market. CutPro offers a return on investment as low as a few months, for many of our clients.
The payback period gets even shorter when more mass production or valuable parts are involved in the production process
How Long Is the Set-Up process for CNC Machine Implementation?
CutPro is one of the easiest products in terms of implementation and training of process planners and machinists. ShopPro is the simpler version of CutPro, and it has built-in video training. CNC Machine operators can learn how to use and implement ShopPro within an hour.
When it comes to advanced process planners and CutPro, it can take just three days of training at their own facility. Alternatively, planners can take our comprehensive 5-day advanced machining engineering course at our well-equipped facilities.
We also provide web-based training sessions and support to our customers. And the best part is, starting from the first trial of our system, you will immediately start enjoying the cost benefits.
Innovation and Product Support
We are closely working with the world-class machining research laboratory at UBC (Manufacturing Automation Laboratory, University of British Columbia) to improve the system with cutting-edge research.
We release software upgrades and optimizations around every 6 months. This helps a CutPro owner benefit from the latest improvements and innovative techniques to be a part of your production process.
MAL Inc. provides technical support with its 20 research engineers. You may always contact us to get more information or support.
Demo and more Product Info
To get more product information, for a demo of the process, or to learn more about our other solutions please contact us using the form below with your needs and objectives. We will get back to you with more information to help you get started with a highly optimized production process.
We never share our customers’ information with others and maintain a neutral position to all industries worldwide.