Testimonials
Jan Bruurs – KMWE, Netherlands
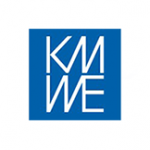
Before we used CutPro we had a lot of problems with defining reliable and economical feeds & speeds, especially for tool assemblies with a large protruding length (> 5× Dc).
MAL provided us a greater understanding and more comprehensive knowledge of machining dynamics.
By using CutPro we are able to achieve a reliable predictability of machining process parameters without any test cuts.
At KMWE we are running tools with a large protruding length up to 8× faster now, even with an increased surface quality on our parts.
The return of the investment was less than a year. In our second year with CutPro, KMWE achieves an estimated annual saving of 2000 hours on machining capacity and rework.
Adam Cange – Boeing, USA
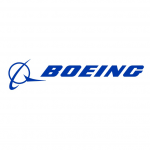
I recently attended the Advanced Machining Course hosted at the University of British Columbia with MAL. Their staff is very technical with advanced machining processes and have helped me better understand the machining process. Besides this, they offer a great software package to optimize and enhance machining performance for all user levels. I would highly recommend attending the Advanced Machining Course at UBC. Thanks!
Mikael Lundblad – Sandvik Coromant, sweden
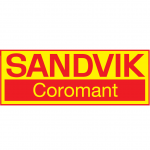
At Sandvik Coromant we use the software CutPro as a powerful tool for analyzing new world leading designs of cutting tools. CutPro is commonly used in our work shops to ensure that tools run at good cutting conditions and that different designs of cutting tools are compared under equal conditions.
Jochem Roukema – ASCO AEROSPACE, CANADA
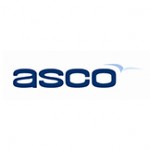
Before we used CutPro to eliminate chatter vibrations, hearing protection was not enough to get operators to setup the parts at the loading station next to the machine. After we optimized the programs, the operators do not need hearing protection anymore, and at the same time the cycle time was reduced by 50%, and tool life improved. Following case studies illustrate the result.
LYLE Hystad – REDLINE PRO MANUFACTURING, canada
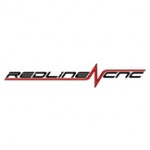
“MAL set up an accelerometer on the part and attached it via USB to a laptop to chart vibration frequency. On the very first set of taps, they recommended we run at 17,000 RPM, and that did the trick. We got rid of the chatter, increased the feed rate, and eliminated the finishing pass. Within minutes of trying this new technology, we’d discovered a way to cut cycle time in half.”
You can read the entire article here.
Dr. Giacomo Bianchi – ITIA National Research Council, Italy
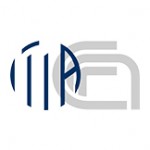
Italian Research Center, MUSP and Spindle Manufacturer Capellini used CutPro and SpindlePro to design high performance and high speed electro-spindle for aerospace industry.
You can read the magazine article (Italian) reporting to the work here.
HartFord Industrial Co. Ltd., Taiwan
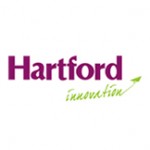
It takes lots of time to meet the customers’ needs when they ask special material or parts machining. After we use CutPro to find the sweet point of machining, it eliminates the chatter vibration and reduces our try-error time. The CutPro really makes money for us.
You can see the illustration of the test process here.
ANDREY SAVILOV, PROFESSOR – Irkutsk State Technical University, Russia
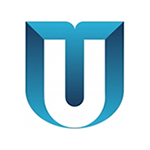
We use CutPro to increase productivity of machining in different areas, especially in aerospace industry. Using CutPro you can get benefits even if you have machine tools with low power spindles and low stiffness.
Next field where we apply MAL software is the cutter design. We can estimate cutting forces and vibrations before machining for different tools. So we save our time and money. The real advantage of CutPro is the opportunity to simulate serrated mills. They are very popular for roughing of aviation components. These cutters have complex construction and geometrics. You can optimize chip breaking geometrics and cutting process for serrated mills with CutPro V10 successfully.
Oliver Tsai – Royal Precision Tools Corporation, Taiwan
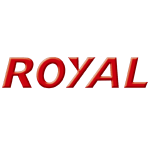
Royal Precision Spindle Manufacturer from Taiwan used CutPro and SpindlePro for the design, performance analysis and dynamic accuracy matching of their spindles.
“We use the CutPro and SpindlePro to predict and design the cutting performance of our spindles. It provides very useful technology information to our customers how to use our spindles. This dynamic stiffness test is a very important procedure to assure all of our spindles with the same quality.
All logos and trademarks are the property of their respective owners.